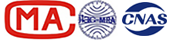
金属表面局部物理或化学性质不均匀的区域。包括非金属夹杂物及其他第二相颗粒、位错或晶界露头、吸附杂质原子、表面空位或台阶等。表面缺陷是原子活性较高的部位,常常成为金属腐蚀的始发处。
硫化后的橡胶制品,有时表面会有疤、起泡、裂口、海绵状、色泽不一致、重皮等缺陷,这些缺陷多半由于硫化压力不足、硫化前表面有污损、胶料硫化速度过快或欠硫过硫等原因造成,为避免出现这些弊病,应严格操作要求,控制好工艺条件。
表面缺陷是制品应力感生的结果,不同的表面缺陷形态有着不同的形成原因,探寻这些原因并加以避免是获得高品质产品的必经之路。对于注塑制品而言,表面缺陷是常见的质量问题。一般,可见的表面缺陷包括开裂、银纹、纹道、波纹、波痕和脆化等。这些缺陷不只会影响制品的外观,更主要的,它们还表明制品的成型过程是失败的。通常,这些表面缺陷是由制品的内外应力超过制品本身的强度而引起的。这种应力感生的缺陷与生产环境、加工工艺及聚合物材料本身有关,有时还涉及到模具或制品的设计。因此,近距离地观察一下制品缺陷的样子,能够帮助我们找到解决问题的方法。常见的表面缺陷各有其自身的特点。例如,纹道(或者波纹、波痕)通常出现在流体的前缘。当流峰出现停顿、压力聚集,接着再向前流动一小段距离,然后再停顿时,就会形成纹道。这种缺陷与流峰压力不足或者注射速度减缓有关。脆化则是由过度充模或充模不足引起的。此外,聚合物的污染或降解,或者接触了环境应力开裂介质等,也会引发脆化问题。开裂既可出现在制品的局部,也可在整个部件上出现。银纹则是由细线或小裂纹引起的发白现象,通常局限在一个小区域上。
通常情况下,表面波纹可能是由以下3种加工问题之一而引起的,包括:压力或体积问题、位置或转移问题,少数情况下也可能是温度问题。一般,对第一阶段充模压力的限制或者对速度控制的不到位是波纹产生的根源。
过低的熔体温度或模具温度是导致缺陷的另一个根源。利用热探针技术或合适的红外传感器可检查熔体的温度,以确保熔体温度处于材料供应商推荐的范围内。对于开裂、银纹或者脆化问题,应寻找与加工相关的应力原因,如注射太快或太慢。注射过快会使分子取向度过高,这对于薄壁制品而言尤其如此。因此,要考虑浇口分布的合理性,以此提供合适的分子取向以及熔接线分布。可以尝试快速和慢速注射制品,从中来观察取向结果。如果制品恰好在脱模后发生开裂或产生银纹,那么最好在制品顶出前对其进行检查,然后彻底减慢顶出速度,看问题是否继续发生。如果问题出在顶出方面,就应看看模具的脱模倒角是否合理。通常,在顶出方向上不恰当的抛光、太高的顶出速度以及顶出区域不够大等,都会引起这类问题。过度充模或充模不足会引起制品的脆化。这是因为,这两种情况都会导致制品内应力过高,特别是在浇口附近。一般,在浇口处的过度充模会引起聚合物链之间被压缩得太紧密。在室温下,过度充模制品的分子链仍会做一点自由移动,但是在低温下,制品收缩则使分子链间挤压过度而导致开裂。通常,堆积过紧的分子链会产生残余压缩应力,使得制品变脆。此外,当浇口附近充模不足时,会引起聚合物分子链在冷却时太松散,导致拉伸应力的产生,从而削弱浇口附近的强度。
要检查充模是否过度或不足,可进行浇口密封分析,以此来确定制品冷却或浇口封闭需要多长时间,同时测试浇口密封和不密封情况下的制品性能(根据应用需要确定)是否有所不同。
此外,热循环检测对于避免制品的翘曲缺陷是十分重要的,因为翘曲缺陷是制品在由热变冷、然后再变热的过程中引发的。因为分子在受力下会试图消除应力,因此热循环会告诉你分子是处于应力状态还是松弛状态。