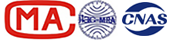
83.060
G40
中华人民共和国国家标准
GB/T9867-2008/ISO4649:2002
代替GB/T9867-1988
zvu81503
硫化橡胶或热塑性橡胶耐磨性能的测定
(旋转辊筒式磨耗机法)
Rubber, vulcanized or thermoplastic-Determination of
abrasion resistance using a rotating cylindrical drum device
(ISO4649:2002,IDT)
CN
ard Das
2008-04-01发布
2008-09-01实施
s/中国国家标准化管理委员会发布
GB/T9867-2008/ISO4649:2002
前言
本标准等同采用国际标准IsO4649:2002《硫化橡胶或热塑性橡胶耐磨性能的测定用旋转辊筒
装置》(英文版)。
本标准等同翻译国际标准ISO4649:2002。规范性引用文件用国家标准取代了国际标准,所引用
的标准内容与国际标准没有差异
本标准根据ISO4649:2002对GB/T9867-1988进行重新修订,为便于使用,本标准做了以下编
辑性修改
删除了国际标准ISO前言。
本标准代替GB/T9867—1988《硫化橡胶耐磨性能的测定(旋转辊筒式磨耗机法)》
本标准与标准GB/T9867-1988相比,主要内容变化如下:
增加了前言
增加了警示语
增加了精密度的内容(本版第10章);
砂布长度由473mm改为474mm±1mm(见5.2)
附录B对1号标准胶配方进行了细微的调整,并对其硫化时间也进行了相应改变;
附录B增加了对1号标准胶硬度的要求
本标准附录A、附录B均为规范性附录
本标准由中国石油和化学工业协会提出。
本标准由全国橡胶与橡胶制品标准化技术委员会橡胶物理和化学试验方法分技术委员会
(SAC/TC35/SC2)归口。
本标准起草单位:西北橡胶塑料研究设计院
本标准主要起草人:朱伟、王朝、赵云鹤
本标准所代替标准的历次版本发布情况为:
--GB/T9867-1988。
GB/T9867—2008/ISo4649:2002
硫化橡胶或热塑性橡胶耐磨性能的测定
(旋转辊筒式磨耗机法)
警告:使用本标准的人员应熟悉正规实验室操作规程。本标准无意涉及因使用本标准可能出现的
所有安全问题。制定相应的安全和健康制度并确保符合国家法规是使用者的责任。
范围
本标准规定了用旋转辊筒装置测定硫化橡胶耐磨性能的两种方法
本标准包括测定试样在一定级别的砂布上进行摩擦而产生的体积磨耗量。方法A用于非旋转试样,
方法B用于旋转试样,试验结果以相对于某种参照胶的体积磨耗量或磨耗指数来表示
注1:由于砂布的级别、生产砂布所用粘接剂的种类以及前面试验的污染、磨损等因素,会导致磨耗损失绝对值的变
化,因此所有的试验都是相对的。与参照胶相比的比较结果既可以表示为与校准过的砂布相比的相对体积磨
耗量,也可以表示为与参照胶相比的磨耗指数。
注2:测定磨耗损失通常统一使用旋转试样,这是由于在试验过程中,试样的整个摩擦表面都会与砂布相接触。不过,
也有相当多的试验使用非旋转试样。
本标准适用于对比试验质量控制、规范依据试验以及仲裁目的、研究和开发工作。可以推断操作过
程与此磨耗试验结果没有紧密联系
2规范性引用文件
下列文件中的条款通过本标准的引用而成为本标准的条款。凡是注日期的引用文件,其随后所有修
改单(不包括勘误的内容)或修订版均不适用于本标准。然而,鼓励根据本标准达成协议的各方研究是否
可使用这些文件的最新版本。凡是不注日期的引用文件,其最新版本适用于本标准。
GB/T531橡胶袖珍硬度计压人硬度试验方法(GB/T531-1999 dt iso7619:1986)
GB/T533硫化橡胶密度的测定(GB/T533-1991, eqv Iso2781:1988)
GB/T2941橡胶物理试验方法试样制备和调节通用程序(GB/T291-2006,ISO23529:2004,IDm)
GB/T6038橡胶试验胶料配料、混炼和硫化设备及操作程序(GB/T6038—2006,IsO2393
1994,MOD
GB/T6379.2测量方法与结果的准确度(正确度与精密度)第2部分:确定标准测量方法重复性与
再现性的基本方法(GB/T6379.2-2004,ISO5725-2:1994,亚T)
ISO9298:1995橡胶配合剂氧化锌试验方法
3术语和定义
下列术语和定义适用于本标准。
3.1
耐磨性 abrasion resistance
抵抗由于机械作用使材料表面产生磨损的性能
注:在本标准中,以校准过的砂布为基准,耐磨性可以用相对于某种标准参照胶的相对体积磨耗量来表示,也可以用
相对于某种参照胶的磨耗指数表示。
3.2
相对体积磨耗量 relative volume loss
参照胶受到砂布的磨耗作用产生一个固定质量损失,在相同的规定试验条件下,试样受到同样作用所
产生的体积损失,以立方毫米mm3)计。
GB/T9867—2008/So4649:2002
注:固定质量损失值被确定为200mg这是由于用方法A及1号标准参照胶(见B2)校准砂布时,此值是校准范围的
中点,而且在9.2相对体积磨耗量的计算中也已积累了相当多的经验。如果已知固定的质量损失值,相对体积磨
耗量也可由方法B旋转试样)或及另一参照胶来计算。[用方法B及2号标准参照胶(见B3)进行试验时,其固
定质量损失值可能为150mg,但其精确度并没有证明已达到使用方法A及1号标准参照胶(见B2)时质量损失
200mg的程度。
3.3
磨耗指数 abrasion resistance index
在规定的相同试验条件下,参照胶的体积磨耗量与试验胶的体积磨耗量之比,通常以百分数表示
注:数值越小,表明耐磨性越差。
4试验原理
本标准是在规定的接触压力和一定的面积上,测定圆柱形橡胶试样在一定级别的砂布上和一定的距
离内进行摩擦而产生的磨耗量。试验中试样可以是旋转的或非旋转的。
磨耗是在圆柱形试样的一端产生(见图1)。砂布包贴在旋转辊筒的表面,试样紧压在带有砂布的辊筒
上,使试样沿辊筒横向移动
单位为毫米
F(10N±0.2N)
1—滑动臂;
5—辊筒,直径150.0mm±
7——试样;
2—滑道
0.2mm,长500mm;
8—试样夹持器;
3——双面胶带;
6-一开口≤2mm;
9-一旋转速度40r/min±1r/min
4一一砂布
图1仪器结构原理图
GB/T9867-2008/Iso4649:2002
测定试样的质量损失并通过试样的密度来计算体积磨耗量。在同一条件下,试验胶的体积磨耗量
与参照胶的体积磨耗量具有可比性
本方法中一个很重要的部分是砂布的制备及使用非旋转1号标准参照胶试样(见B.2)对砂布进行
的校验。
5试验装置和材料
5.1磨耗机
磨耗机由固定砂布(5.2)的旋转辊筒和可水平移动的试样夹持器组成,见图1。
辊筒直径为150.0mm士0.2mm,长约500mm,以40r/min士1r/min的速度旋转,旋转方向如
图1所示。
试样夹持器是一个有开口的圆筒,其直径可在15.5mm~16.3mm范围内调节,并有一个调节试
样伸出长度的装置,使试样伸出夹持器的长度为2.0mm±0.2mm。夹持器安装在旋转手柄上,该手柄
与一个可以在滑杆上水平移动的滑道相连。当辊筒旋转一周时(见本条的注1),夹持器应水平移动
4.20mm±0.04mm。在试验过程当中,通过夹持器的旋转使试样旋转(方法B),夹持器适宜的转速为
辊筒每旋转50r夹持器旋转1r。
注1:试样水平运动时可四次经过砂布的任意部位
夹持器的中心轴线应与辊筒旋转方向垂线有3倾角(见图1),夹持器中心轴应位于辊筒水平轴正
上方,其偏差应不大于士1mm。
试验中滑动臂和试样夹持器应没有振动,用10N±0.2N的垂直作用力将试样紧压在辊筒上。出
于特殊要求,也可使用5N±0.1N的垂直作用力。
注2:一般对硬度低于约40IRHD的橡胶施加外力为5N
用三根双面胶带沿辊筒全长间隔均匀地将砂布固定在辊筒上,未被试样接触到的辊筒边缘宽度相
等。应确保砂布牢固地包贴在辊筒表面上,以使整个辊筒表面形成一个均匀一致的摩擦面。其中一条
双面胶带应固定在砂布接头处,砂布接头之间应紧密粘接,空隙宽度不应超过2mm。胶带宽约
50mm,厚度不大于0.2mm
将试样放在砂布上的运行起点处,当磨损行程达40.0m士0.2m(相当于84r)时,自动停机。在试
样磨耗量较大时,磨损行程可减少至20.0m士0.1m(相当于42r)。因此,应优先采用转数器或自动关
机装置。
注3:对于磨耗量相当高的橡胶,可使用10m的行程
为保护砂布,防止其受到试样夹持器的损坏,建议安装一个装置,在试样夹持器边缘接触到砂布前
能自动停机。
试验设备应安装吸尘软管和刷子以清除其表面上的胶屑
5.2砂布
砂布由粒度为60号的氧化铝组成,砂布宽度最小为400mm,长474mm±1mm,平均厚度为
1mm。
在此砂布上使用非旋转1号标准参照胶(见B.2)进行试验,当磨损行程为40m时,磨耗量应在
180mg~220mg之间。
每张砂布首次使用时,应标明运转方向。每次试验都必须与标明的运转方向一致
注:对砂布的要求见附录A
5.3旋转裁刀(见图2)
非模具硫化的试样制备可以用图2所示的旋转裁刀。对于多数橡胶,裁刀的旋转速度最少为
1000r/min,对于硬度低于50IRHD或邵尔A50的橡胶,旋转速度应更高。
GB/T9867-208/Iso4649:2002
单位为毫米
四
NIE
Da2团
中16.2
中16.3-005
∮16.6-0,05
图2制备实验试样的裁刀示意图
5.4天平
用精度为士1mg的天平称量试样的质量
5.5标准参照胶
对标准参照胶的详细说明见附录B
6试样
6.1试样规格和制备
试样为圆柱形,其直径为16.0mm士0.2mm,高度最小为6mm
试样的制备通常用裁刀或其他旋转切割工具从硫化胶片上裁取。裁切时可在裁刀的刃口上用添加
润滑剂的水进行润滑,不允许冲裁试样。
另外,试样也可以用模具硫化成型。
如果试样高度达不到要求时,可将试样粘在硬度不低于80邵尔A的基片上,但橡胶试样高度应不
小于2mm
6.2试样数量
对于每个试验胶至少进行3次试验,每次试验都应使用一个新试样。出于仲裁目的,用10个试样
对于1号标准参照胶(见B2)和2号标准参照胶(见B.3),为减少损耗,一个试样可进行3次试验
6.3硫化或成型与试验之间的时间间隔
对于所有试验,硫化或成型与试验之间的时间间隔最短是16h。对于非产品试验,硫化与试验之
间的时间间隔最长是4周。比较试验应尽可能在相同的时间间隔内进行。对于产品试验,只要有可能,
试验与硫化之间的时间间隔不得超过3个月。在其他情况下,试验应在需方从收货日期算起的2个月
内进行。
6.4环境调节
所有试样试验前应按照GB/T2941的规定,在标准实验室温度下调节至少16h。
注:对于一些对湿度较敏感的橡胶,还应控制环境湿度
GB/T9867-2008/O4649:2002
7试验温度
试验应在标准实验室温度下进行(见GB/T2941)
在试验进行当中,磨损表面温度上升可导致试样表面升温。在本标准中,试验开始前及试验过程中
的温度为环境温度时,这种温升可忽略不计
8程序
8.1试验步骤
在每次试验前,用毛刷去掉砂布上此前试验留下的所有胶屑,推荐毛刷为直径55mm,由长约
70mm的硬尼龙或同类硬毛(见本条的注1)制成。在某些情况下,用一个参照胶(见本条的注2)进行空
白实验,可对砂布起到有效清洁作用(见本条的注3)。
注1:不推荐使用可减少砂布使用寿命的金属刚毛
注2:仅用于清洁目的的参照胶不必满足测试用标准参照胶的严格要求
注3:一些实验室发现将橡胶胶屑吹走比刷掉更有效。当吹风枪喷嘴被阻塞时,出于安全考虑,给吹风枪所施压力
最大为0.2MPa,一般补给空气压力在0.5MPa到0.9MPa之间为宜。
方法A使用非旋转试样,方法B使用旋转试样。用1号标准参照胶(见B.2)、2号标准参照胶(见
B.3或指定参照胶作为参照胶。因所得结果可能不同,所以试验报告中应注明所用试验方法和使用的
参照胶。用于比较目的的试验,对于所有的试验胶和参照胶均应采用相同的试验条件。
试样的质量应精确到1mg。将试样放入夹持器中,使试样伸出夹持器的长度为2.0mm土
0.2mm。长度可通过标准尺来测量。
用10N士0.2N的垂直作用力将试样紧压在辊筒上,特殊情况下压力可减至5N士0.1N但需在
试验报告中注明
如果有通风装置,将它打开。把带有试样的夹持器从滑道移至辊筒的起点处,开动机器进行试验。
检查试样夹持器的振动情况。如果试样夹持器振动较反常,那么试验结果没有意义。磨损行程达40m
时自动停机。当出现较大的磨耗量时(通常40m行程时大于400mg),试验可在20m行程时停止,然
后将试样伸出长度重新调至2.0mm士0.2mm后,再进行试验以便完成剩下的20m行程。试样高度
任何时候也不能少于5mm。若在40m行程内,试样磨耗量大于600mg,试验只需进行20m,并应在
报告中注明,将此时磨耗量乘以2,从而得到40m行程时的磨耗量
对于试验中运行着的非旋转试样,应确保试样以同样的方式位于夹持器的同一位置上。
对于被粘接的试样,试验时注意不要将其磨到试样的粘接线上。(如有必要,使用20m行程)。
试验结束后,称取试样的质量,精确到1mg。有时,在试验后,试样的一处小胶边可能会被扯下,尤
其是对于非旋转试样而言
对于同种胶样的试验应连续进行。
8.2与标准参照胶或指定参照胶之间的比较
试验胶与附录B中规定的两种标准参照胶之一或指定参照胶间进行比较。
参照胶质量损失的测定,按照8.1规定的试验步骤,在每次用试验胶进行系列试验之前和之后都要
进行,至少进行3次试验。在每一系列试验中,试验胶的试样最多进行10次试验。在两个系列试验间,
不要断开在同一个试验胶上进行的各次试验行程。在一种标准参照胶的同一试样上进行重复试验时,
为使整个试样的温度恢复到标准实验室温度,允许在每次试验间有充足的停放时间。
对易于附着的试验胶,在每次试验胶进行试验后,都要进行参照胶的质量损失的测定。在附着严重
的情况下,参照胶在试验后的质量损失与试验前的质量损失有较大减少,这是因为砂布被参照胶“清
洗”,而不是参照胶被砂布磨损。如果参照胶的质量损失减少大于10%,此方法无效。
为克服这一问题,已提议变更本试验方法,包括使用40号粒度的砂布。任何这样变更的应用应得
到专业标准化技术委员会认可,并在试验报告中详细注明[见第11章c)4)]
GB/T9867-2008/ISO4649:200
8.3密度
按GB/T533规定的方法分别测定参照胶与试验胶的密度
结果表述
9.1概述
试验结果可以用相对体积磨耗量或磨耗指数来表示。
分别计算试验胶质量损失的算术平均值△m:和参照胶质量损失的算术平均值
△mn
9.2相对体积磨耗量,△Vm
相对体积磨耗量(见3.2),mm3,按式(1)计算
△Vd=(△m:×△m。on)/(AX△m1)
(1)
式中
△m:—试验胶的质量损失值,mg;
△mam参照胶的固定质量损失值(见3.2),mg;用方法A及1号标准参照胶(见B.2)测得的固定
质量损失值200mg;
P—试验胶的密度,mg/mm3;
△m,一参照胶的质量损失值,mg
注:对于此种结果表示方法,通常采用1号标准参照胶。
9.3磨耗指数,ARI
磨耗指数(见3.3),%,按式(2)计算
ARI=(△m1×P1)/(△m1×p)×100………(2)
式中:
△m1参照胶的质量损失值,mg
P—参照胶的密度,g/cm3;
△m;试验胶的质量损失值,mg
试验胶的密度,g/cm
10精密度和偏差
10.1对于在多个实验空间进行试验所得的试验结果的精密度和偏差应与GB/T6379.2规定的一致。
10.2精密度结果可判断在特定的多个实验室间使用相关材料按如下规定试验程序,进行试验方法的
精密度。如果没有有关参数适用于此材料和具体试验方法的记录,此材料就不能适用于精密度参数的
试验当中
10.3国际间多个实验室间试验程序在1986年由16个参加实验室共同进行,试验中在不同的磨损程
度上使用5种不同的硫化橡胶。由一个实验室硫化橡胶胶片,每个参与实验室从这些胶片上裁取试样
对每种胶料在相隔3d~4d的两个试验日中,每个试验日进行3次磨耗试验的测量,试验结果为3个独
立试验的结果。
10.4在表1到表3中给出精密度结果,表中所用符号r、(r)、R、(R)定义如下
绝对重复性,用测量单位表示
(r)相对重复性,用百分比表示;
R绝对再现性,用测量单位表示
(R)相对再现性,用百分比表示
10.5每个试验方法的精密度可以用如下陈述的“特定值”来表示,这些值是在使用试验方法的试验结
果中得到的。这些特定值是数值r、(r)、R、(R),表1、表2、表3所示有关的平均值,接近于常规试验操
作研究中的平均值
GB/T9867-2008/SO4649:2002
表1方法A非旋转试样,1号标准参照胶(见B.2)
实验室内
试验胶
实验室间
平均相对体积磨耗量/mm
(r)
R
(R)
A(NR/BR)
9.6
18.8
27.6
B (NR/SBR)
106
10.8
10.2
21.4
C (NR)
160
23,2
14.5
30.4
19.0
D (IIR)
257
30.2
11.8
57.5
22.4
E (EPDM)
34
39.8
11.5
83.0
24,1
表2方法A非旋转试样2号标准参照胶(见B.3)
实验室内
实验室间
试验胶
平均相对磨耗指数/%
(r)
R
(R)
(NR/BR)
157
59
B (NR/SBR)
15,0
14.7
19.1
8.7
C (NR)
9.1
13.6
13.6
20.3
D IIR)
18,4
10.2
23.7
E (EPDM)
11.9
7.2
22.5
表3方法B旋转试样,2号标准参照胶(见B.3)
实验室内
实验室间
试验胶
平均相对磨耗指数/%
(r)
R
(R)
A (NR/BR)
144
20.2
14.0
45,8
3.8
B (NR/SBR)
101
9.6
9.5
15.9
15,7
C NRY
11.0
15.5
D (IIR)
43
7.9
5.3
12.3
E (EPDM)
34
9.7
7.2
21.2
10.6重复性——这些试验方法的绝对重复性r为表1、表2或表3中的表列值。在规定的同一试验条
件下得到2个单独的试验结果,其与表列值r(任意已知值)的差异不止是来自不同的抽样。
10.7再现性—这些试验方法的绝对再现性R为表1表2或表3中的表列值。在两个不同的实验
室间规定的同一试验条件下得到2个单独的试验结果,其与表列值R(任意已知值)的差异不仅仅是来
自不同的抽样
10.8重复性和再现性是以平均试验结果的百分数来表示,(r)和(R)相当于对r和R的应用说明。
(r)和(R)2个单独试验结果的差异是用其2个试验结果算术平均值的百分数来表示的。
10.9试验方法术语当中,偏差是测量的试验结果均值与公认的参照值或标准值之差。因为试验方法
已专门限定磨耗量,那么就不存在参照值,因此就不能确定偏差。
GB/T9867—2008/KSo4649:2002
11试验报告
试验报告应包括下列内容:
a)使用标准;
b)试样的详细说明
1)试样来源和说明
2)对混炼胶的具体说明和硫化成型条件,若已知;
3)试样制备的方法,是裁切还是模压
c)试验的详细说明
1)标准实验室温度;
2)使用的试验方法(方法A或方法B);
3)使用的是1号标准参照胶(见B.2)2号标准参照胶(见B.3),或指定参照胶
4)任何与常规试验程序的差异,特别是如果试验只运行磨损行程的一半或只施加一半垂直
作用力(见8.2最后一段);
d)试验结果:
1)相对体积磨耗量的平均值或/和磨耗指数的平均值;
2)试验结果的标准偏差(可选);
3)试验胶和参照胶的密度
)试验日期。
GB/T9867-2008/ISo4649:2002
附录A
(规范性附录)
有关砂布的说明
砂布由粒度为60号,即能穿过60号筛孔的氧化铝颗粒组成,用酚醛树脂作粘合剂粘到斜纹布上。
这种砂布使用非旋转试样,用附录B中的B.2中规定的1号标准参照胶进行试验。若砂布产生的磨耗
量大于300mg,必须用钢制试样预磨一次或两次,使磨耗量减少到200mg~220mg之间,分别用两个
试样来进行校准试验。砂布上应注明运转方向,各次试验都必须与标明的方向一致
经验证,在磨耗量降到180mg以前,1号标准参照胶(见B.2)使用此类型的砂布可运行至少几百
次试验;降到180mg以后,就应换掉砂布
用此方法生产的标准砂布在市场有售。
注:若需提供可比较的结果,可以用砂纸代替砂布。
GB/T9867-2008/ISO4649:2002
附录B
(规范性附录)
标准参照胶和指定参照胶
B.1用途
由于此项磨耗试验是比较性试验,因此参照胶很重要。参照胶的性能对试验的重复性和再现性影
响很大。
B.2中规定的标准参照胶用于砂布(5.2)的校准,使用方法A是因为在此应用上已得到相当多的
经验。它也可作为比较标准参照胶用于试验方法A和方法B中。1号标准参照胶可通过市场得到。
B.3中规定的参照胶为一种典型的轮胎脍面橡胶,并在使用中作为标准参照胶,其中包括第10章
规定的多个实验室间进行的试验程序。2号标准参照胶通常由使用者制备,对于那些没有条件制备试
样的使用者,也可通过市场得到。
使用者也可按照个人需要来指定其他参照胶,但应注意试验结果的重复性和再现性。在试验报告
中应注意不能把指定参照胶和1号或2号标准参照胶混为一谈
B.2用于校准砂布和作为相对标准参照胶的1号标准参照胶
B.2.1配方
1号标准参照胶的配方见表B.1。
表B.11号标准参照胶配方
材料名称
质量份数
天然胶(SMRL)
100.0
氧化锌,等级B4c(见ISQ9298:1995,附录D)°
N异丙基N-苯基对苯二胺(IPPD)b
1.0
二硫化二苯并噻唑(MBTS)°
炭黑N3304
36.0
碗磺
2、5
合计
191.3
格瑞尔-威克公司
b拜耳公司;
拜耳公司;
d德固萨公司。
假如试样满足B.2.4的要求,也可使用等效的材料。
B.2.2混炼程序
如下混炼程序满足要求。假如标准离差低且性能符合B.2.4的要求,也可使用其他程序。用密炼
机混炼所有材料,程序按表B.2规定进行。之后,按表B.3规定,用开炼机将混炼胶搅拌均匀。
10
GB/T9867-2008/So4649:2002
表B.2密炼机混炼程序
混炼室容积:4.6L(通过小麦颗粒或其他适宜方法测量)
混炼室填充度:65%士5%
速度:30r/min
有效冷却
橡胶质量:2000g
加料顺序
时间/min
加入橡胶
加入氧化锌、防老剂、促进剂
7.5
加入炭黑
加入硫磺
排料
18
最终胶料温度:100℃到110℃
表B.3开炼机混炼程序
辊筒直径:250mm
工作宽度:400mm
辊筒表面温度:50℃±5℃
辊筒转速:约12.4r/min和18.1r/min
混炼步骤
时间/min
辊距/mm
母炼胶包辊
0.5
切割3~4次
翻转辊压胶片
出片关机
10
出片最终温度:约70℃
B.2.3硫化
胶片厚度最少为6mm。将胶片插入预热至150℃±2℃模具中,并置于平板机上施加压力数下,缓
缓加压到至少为3.5MPa并硫化25min1min。推荐的硫化胶片尺寸为8mm×186mm×186mm,
每张胶片大约可裁取90个试样。
B.2.4性能要求
B.2.4.1概述
B.2.4.2、B.2.4.3和B.2.4,4中规定的性能控制程序,可使磨耗量达到一致的水平
硫化与试验之间的时间间隔最短应为16h,最长应为7d
B.2.4.2参照试样
按6.1的规定,从足够多的硫化胶片上,每片裁取一个试样,以为将来试样生产的质量控制提供参
照试样。这些试样可按B.2.5中规定进行贮存,贮存可长达3年。
B.2.4.3质量损失
为质量控制而进行的质量损失测定,应使用一张专用的砂布。用15个参照试样对砂布进行校准
每次用非旋转试样运行3次,以所得测量值的中值作为每一试样的质量损失。这15个中值的平均值
△mRd应在180mg~220mg之间。
GB/T9867-2008/ISo4649:2002
每到第5个“生产过程”执行此程序。每个“生产过程”包括由相同操作者在相同的条件下,在1d
c》
2d的时间内进行几个批次操作
个生产过程质量损失△mpod是通过其中个有代表性的胶片来确定的。按6.1中规定,从这张
胶片上裁取15个试样,测量每个试样的质量损失,用非旋转试样进行3次并报告其中值。用这15个中
值计算△mpm和标准偏差。△mpm与最近的△mx之差不能大于15mg
为确保质量统一,特别建议:用市场上获得的参照试样进行首次校验。有时也可晚些进行。厂内生
产的试样△m与市场上获得的试样△mk之差不应超过10mg
B.2.4.4硬度
按GB/T531的规定测量邵尔硬度,在每个胶片上最少测量4处,并报告其中值。
生产过程中所有试片的硬度(即所有中值)平均在邵尔A60士3
B.2.5贮存
胶片应放在冷暗处贮存,并将防止其氧化(例如聚乙烯)的材料包裹在胶片上。
B.3作为相对标准参照胶的2号标准参照胶(典型的轮胎胎面橡胶)
B.3.1配方
2号标准参照胶的配方见表B.4。
表B.42号标准参照胶配方
材料名称
质量份数
天然橡胶(SMRL)
100.0
硬脂酸
氧化锌
N330炭黑
50.0
N异丙基N-苯基对苯二胺(IPPD)
环己基苯并-2噻唑次磺酰胺(CBS)
0.5
硫磺
2.5
合计
161.0
B.3.2混炼及硫化
用于制备、混炼和硫化橡胶的程序与设备,应按照GB/T6038的有关规定。可使用密炼机或开炼
机。胶片的硫化温度为140℃,硫化时间为60min。
B.3.3贮存
标准参照胶应放在冷暗处贮存,并将防止其氧化的材料(例如聚乙烯)包裹在胶片上
B.3.4性能要求
两个不同批次的标准参照胶的质量损失值之差,按第8章规定应在士10%以内。
版权专有侵权必究
书号:155066·1-31552
GB/T9867-2008
定价
16.00元
中华人民共和国
国家标准
巯化橡胶或热塑性橡胶耐磨性能的测定
旋转辊筒式磨耗机法)
GB/T9867—2008/ISO4649:202